studying the effects of impact loading shock loading and thermal loading on vertical fiber optic spl
Innovation is our strength
STUDYING THE EFFECTS OF IMPACT LOADING, SHOCK LOADING AND THERMAL LOADING ON VERTICAL FIBER OPTIC SPLICE CLOSURE USING FEA
Engineering Design & Drafting | CAE Services: CFD & FEA | Reverse Engineering | Rapid Prototyping | Product Design | Value Engineering | PLM Services | Technical Documentation
Case Study Highlights
EFFECTS OF IMPACT LOADING, SHOCK LOADING AND THERMAL LOADING ON VERTICAL FIBER OPTIC SPLICE CLOSURE USING FEA
The Client
- Industry : Communication Products Manufacturer
The Objective:
- Evaluating vertical fiber optic splice closure for structural strength during impact loading, shock loading and thermal loading through finite element approach.
The Solution:
- A 3D assembly model was developed for the fiber optic closure and finite element simulations were performed using impact loading, shock loading and thermal loading conditions as required by the client. The results identified critical stress and deformation regions and were found within permissible limits.
The Challenges:
- 3D modeling accuracy to capture accurate physics during loading conditions
- Ensuring proper application of boundary conditions for number of virtual tests including impact loading, shock loading and thermal loading
- Maintaining accuracy and appropriateness of the FEA results to minimize physical test trials
The client is a manufacturer of various electronics & communication related products and equipment such as cables, sensors, closures etc. Their new design for splice closure needed to be validated virtually under number of loading conditions. The manufacturer as such approached Australian Design and Drafting Services to shorten their development time and seek expert help for virtual simulation testing.
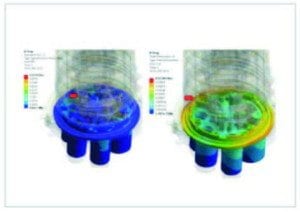
The Solution:
- The software used to perform analysis was ANSYS v14.5 Professional NLS. A 3D Assembly model of Splice Structure was created and analyzed for Various Tests: Shock Loading, Impact Loading (Equivalent Static Loading), Temperature Loading etc. The analysis was performed to determine whether the structure will withstand the Tests performed.
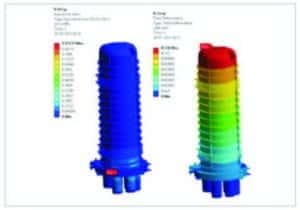
Benefits:
- Shortened product development time
- Reduced cost and time required in physical test trials
- Provided opportunity to modify design for future applications
About Australian Design And Drafting Services
Australian Design and Drafting Services is a specialist firm providing engineering solutions to organizations across the globe. We have extensive experience in providing concept to manufacturing and post-manufacturing solutions to clients with a team of expert design engineers, CAD professionals and simulation analysts. We are based in Australia, serving 24×6, with a world-class infrastructure, hardware and software capabilities to address complex engineering problems with least turn around time.