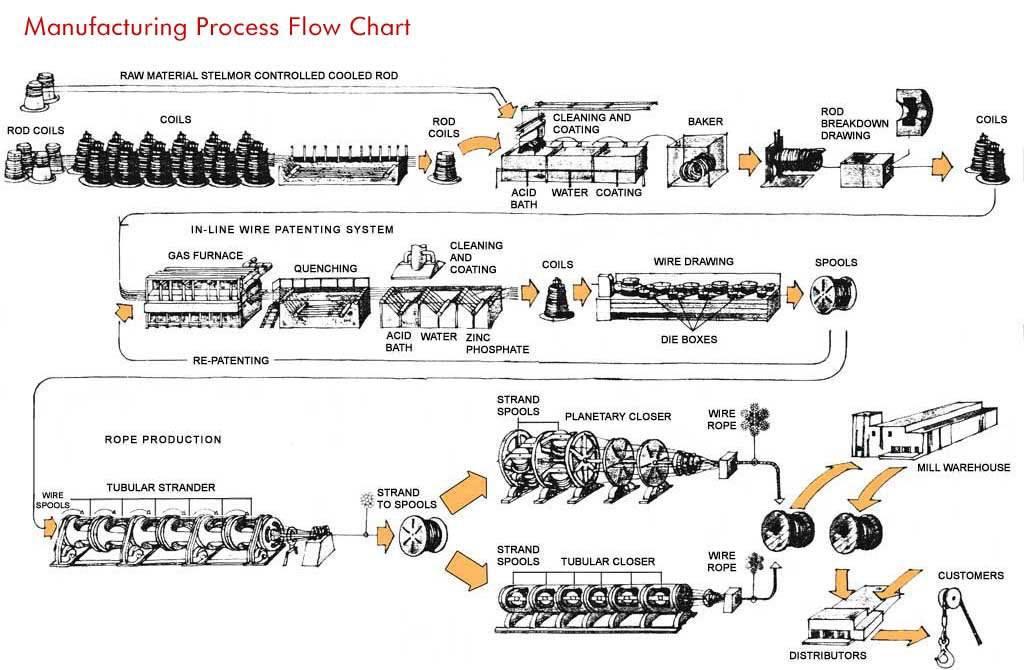
At Australian Design & Drafting Service, we support our customers through production planning, which is at the core of all manufacturing processes. We, as a team, craft the most potent way to manufacture quality products and make the best use of the current resources during the manufacturing process. Our project manager has years of experience in minimizing costs and time to market and increasing the workplace’s efficiency.
Our manufacturing services use each aspect of the manufacturing and production process, from the conceptual design stage to reach the final manufacturing and testing stage. We use best practices and offer customized plans for product development. Our team use a perfect blend of available software tools to provide the best services and solutions. Our techniques help to become leaner in more efficient business.
MANUFACTURING SUPPORT AND PROCESS PLANNING
- Production or manufacturing process planning: It is perhaps the most critical part of a production process. We guide through each stage of the production process.
- Concept planning: Our team of mechanical engineers help you begin with the concept planning stage. We guide you through the risk versus reward analysis of a new product lifecycle.
- Financial planning: We provide you with the necessary financial planning by estimating the future value of the proposed product. Our team help you decide how much you should invest for a fair future return.
- Product planning: Planning the actual product is the key to success. Our mechanical engineers analyze market information and ensure that the proposed development answers a critical market necessity. It’s not an attempt to enter an already overcrowded sector.
- Production planning: It is the most cost-intensive project stage, selecting suitable facilities, the right supplier, and fair labor. It is a critical part to get success of the project. Therefore, we ensure to make the right choices the first time.
- Process planning: After helping with product planning, our experienced team ensure that the right clientele sees the product. Our processes are managed efficiently enough to meet the demands of the customer in time.
- Manufacturing support: Our manufacturing support systems offer you the necessary post-production support to efficiently operate the project and smooth out any unexpected hiccups. The terms of the initial agreement will define the period of support.
Other than assisting customers with the new production process, we provide several other services as well like:
- Cost estimation: Our experienced team of cost estimators provides cost estimate information. It includes a bid for a contract, decides on a project’s profitability, or even decides on a product. Based on factors like materials and machinery requirements, location and time requirements, and labor and software requirements. Our cost estimators offer study data and present the required information.
- Process innovation: The in-house team at Australian Design & Drafting offers experienced in launching brand new ideas in the market. It helps to evaluate the technical and commercial merits and demerits of any innovative process that you plan to implement.
- Environmental knowledge: Implementing any product plan without considering the possible impact on the environment would be a foolhardy endeavor today. We are informed about the environmental regulations that govern the manufacturing process. Our team guide you in case laws are flouted.
MANUFACTURING SUPPORT AND PROCESS PLANNING
Manufacturing support and process planning are critical aspects of industrial operations that focus on optimizing production processes, improving efficiency, and ensuring the successful execution of manufacturing activities. Here’s an overview of manufacturing support and process planning in industries:
- Production Planning: Develop a comprehensive production plan that outlines the sequence of manufacturing operations, resource requirements, and scheduling considerations. This plan considers factors such as production volumes, available resources, lead times, and customer demand.
- Process Selection: Determine the most suitable manufacturing processes and techniques for producing the desired products. Consider factors like product complexity, volume, quality requirements, cost-effectiveness, and available equipment and technology.
- Facility Layout and Design: Optimize the layout of manufacturing facilities to facilitate smooth material flow, minimize bottlenecks, and maximize operational efficiency. Consider factors like equipment placement, workflow, safety regulations, and space utilization.
- Equipment and Tooling Selection: Identify and select appropriate machinery, equipment, and tooling required for manufacturing operations. Consider factors such as production volume, product specifications, quality requirements, maintenance needs, and cost-effectiveness.
- Supply Chain Management: Coordinate with suppliers to ensure the timely availability of raw materials, components, and other necessary inputs. Efficient supply chain management helps prevent production delays and optimize inventory levels.
- Workforce Planning: Determine the required workforce, including skilled labor, operators, technicians, and engineers. Consider training needs, skill sets, staffing levels, and workforce optimization strategies.
- Quality Assurance: Develop and implement quality control measures to ensure that products meet the required quality standards. This includes establishing quality control checkpoints, conducting inspections, implementing testing protocols, and implementing corrective actions.
- Process Optimization: Continuously analyze and improve manufacturing processes to enhance efficiency, reduce waste, and increase productivity. This involves identifying bottlenecks, eliminating non-value-added activities, implementing lean manufacturing principles, and applying automation and digital technologies.
- Standard Operating Procedures (SOPs): Establish clear and standardized procedures for each manufacturing operation. SOPs provide guidelines for operators, ensuring consistency, quality, and safety in the production process.
- Manufacturing Support Systems: Implement software systems and tools to support manufacturing operations, such as Manufacturing Execution Systems (MES), Enterprise Resource Planning (ERP) systems, and data analytics platforms. These systems help monitor production progress, track inventory, manage resources, and provide real-time insights for decision-making.
- Continuous Improvement: Foster a culture of continuous improvement by encouraging employee involvement, implementing feedback mechanisms, and embracing innovation. Regularly review and evaluate manufacturing processes to identify areas for enhancement and implement necessary changes.
Manufacturing support and process planning aim to streamline operations, optimize resource utilization, ensure quality, and meet production targets. Industries can achieve efficient and cost-effective manufacturing processes by implementing effective strategies and leveraging technological advancements.